Pharmaceutical
Data Integrity & Line Integration- To overcome legacy technology barriers and solve diverse machine connectivity issues with PLC and HMI systems.
Overview
This pharmaceutical giant manufactures and sells pharmaceutical formulations and active pharmaceutical ingredients (APIs) and is among the top 3 companies in India and the top 10 in the world in this category. Overcoming legacy technology barriers, implementing effective compliance, and solving water system’s data integration, ensuring quality and compliance while facing connectivity challenges.
Our solutions included network hardware, DLR ring architecture, SCADA software for centralized monitoring, and 21 CFR part 11 compliance for HMI/SCADA systems.
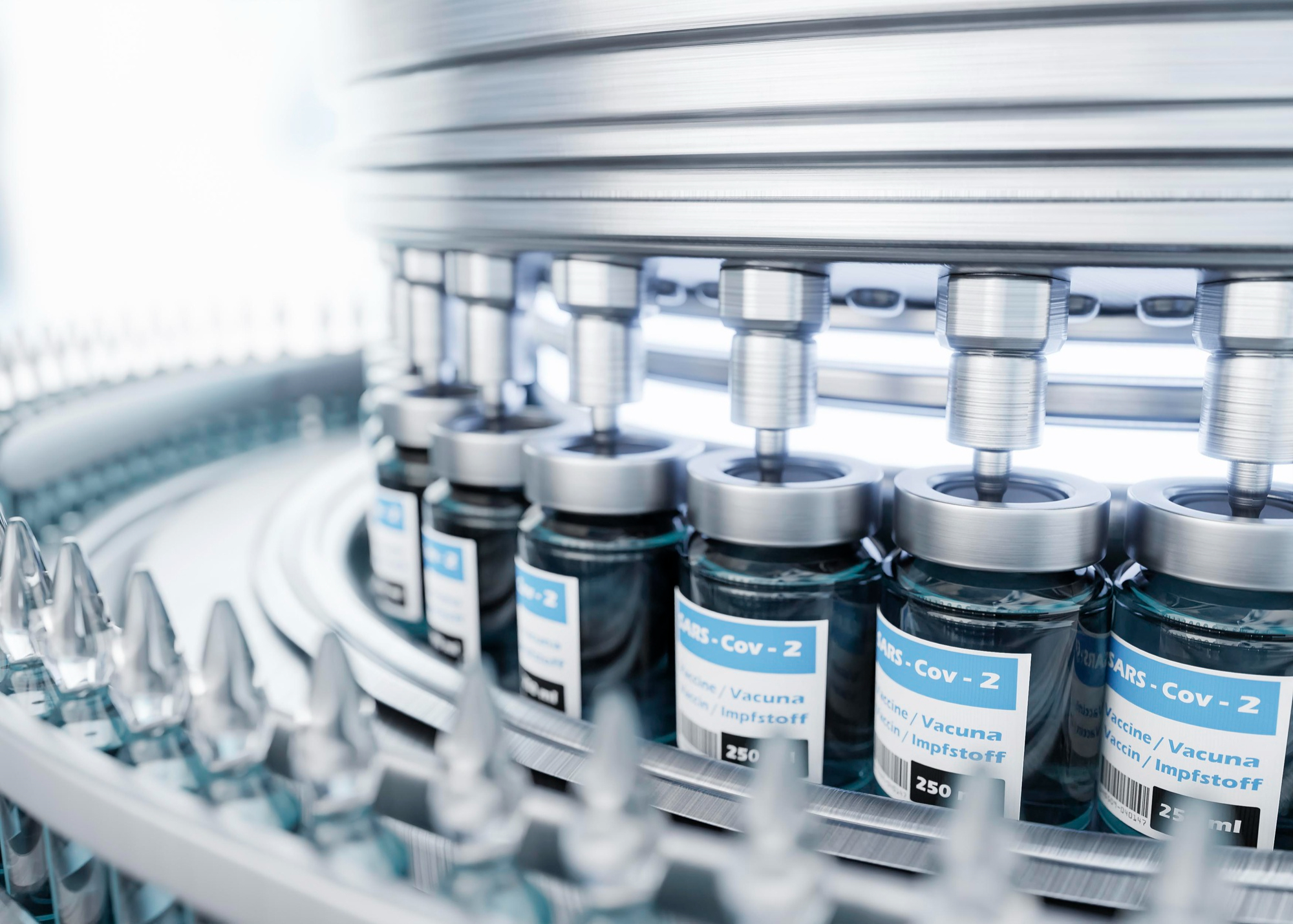
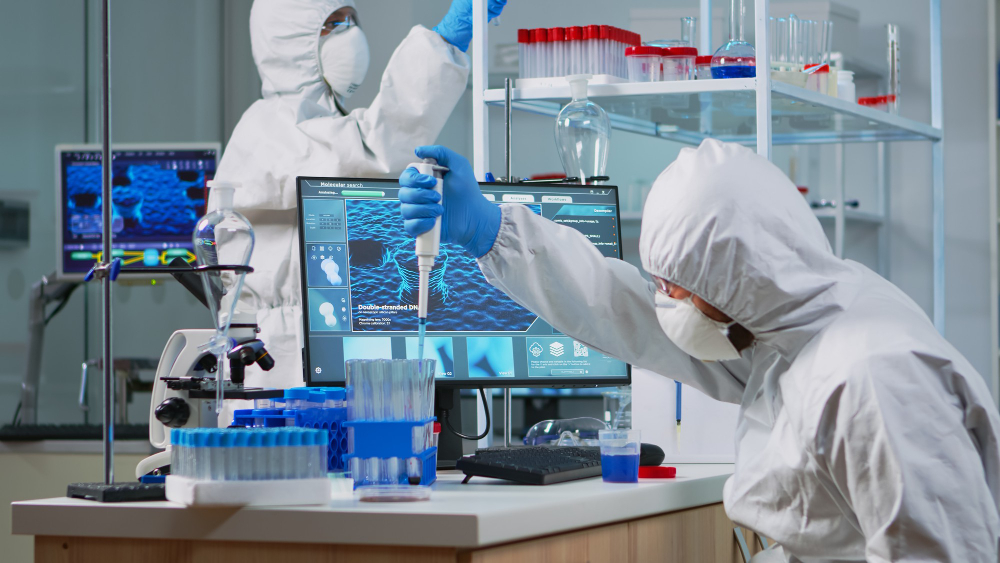
Benefits of Services
Our team successfully overcame the diverse machine connectivity issues with PLC and HMI systems. Leveraging Rockwell Automation’s platform, we delivered top-tier visualization and reporting, while meticulous planning ensured optimal machine uptime. Rigorous system validation ensured compliance with client requirements.
- Integrated all machines to a central SCADA for monitoring and reporting.
- Standardization of Batch Process.
- Easy retrieval of historical data.
- Connectivity to MEC/ERP/MIS system.
- Integrity of batch data for compliance requirements.
Want To Know More?
The Impact We Create
Efficiently solved connectivity issues with PLC and HMI systems with Data Integrity & Line Integration
The problem of overcoming legacy technology barriers was solved with network hardware, DLR ring architecture, 21 CFR part 11 compliance for HMI/SCADA systems and a lot more to achieve the target outcome.
Increase In
Easy Retrieval of Historical Data
Increase In
Standardization of Batch Process
Reduction In
Human Error
Increase In
Proactive Approach
FAQs
Challenges included integrating different PLCs with various protocols, ensuring machine availability for modification and validation, and achieving data integrity and compliance as per 21 CFR Part 11.
Proper planning and project scheduling were the keys to ensuring machine availability for ensuring necessary modifications and validations.
21 CFR Part 11 is essential for data security and integrity in the pharmaceutical industry, ensuring electronic records authenticity and integrity.
Hardware, such as Ethernet connectivity, was added to each PLC to enable effective data sharing.
The DLR ring structure was employed to guarantee data availability even during network disruptions.
SCADA software was utilized for central monitoring and reporting, including features like batch reports and audit trails.
Benefits include integration of all machines into a central SCADA system for monitoring, standardized batch reports, easy retrieval of historical data, and connectivity to the MES/ERP/MIS system.
Our team’s expertise and Rockwell Automation’s platform were instrumental in overcoming connectivity challenges and ensuring client expectations for visualization and reporting were met.
Modifying Standard Operating Procedures (SOPs) is crucial to align system operations with the project’s objective and compliance requirements.
Data integrity compliance was maintained through rigorous validation of the complete system, ensuring it met the client’s compliance requirements.
TECHNOLOGY PARTNERS


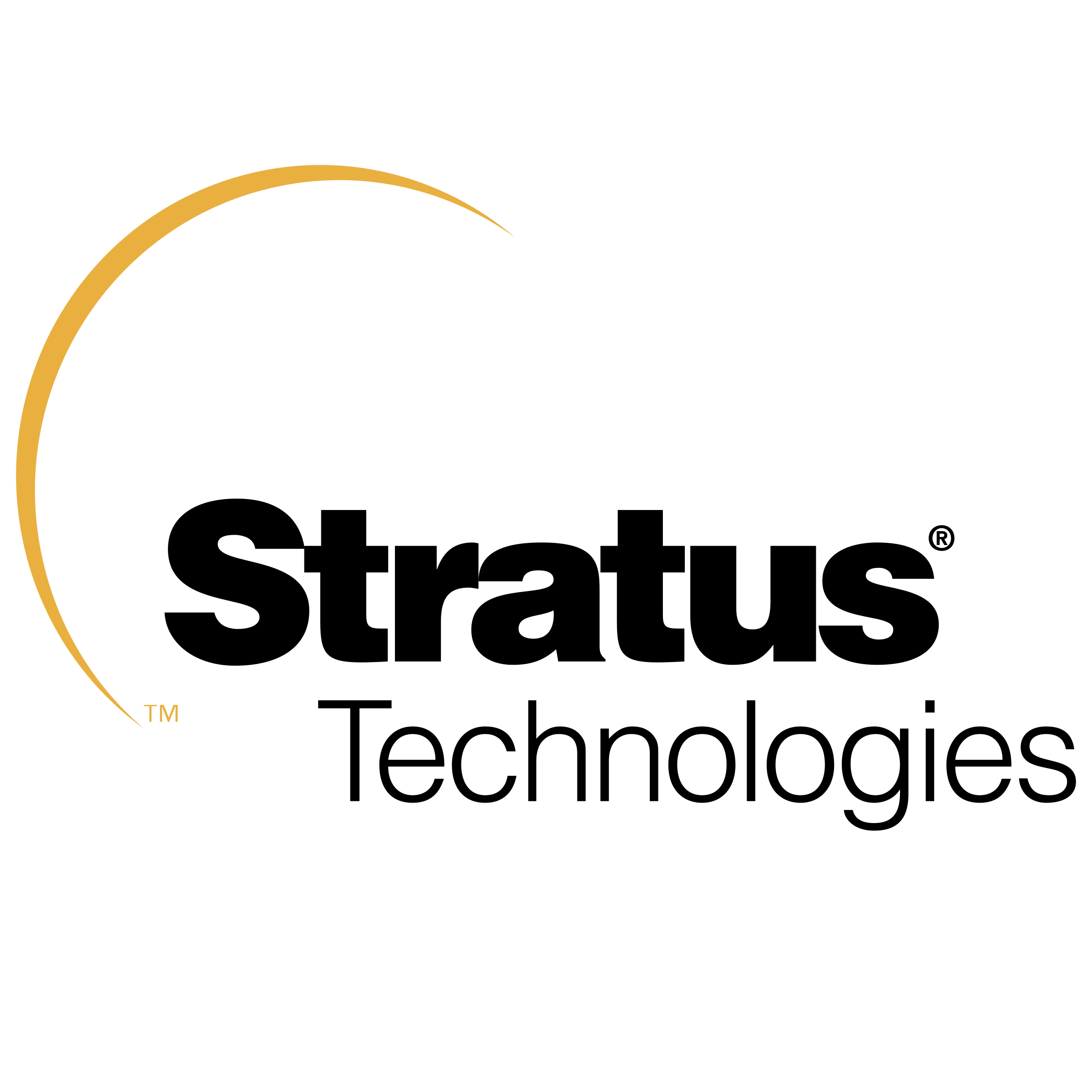
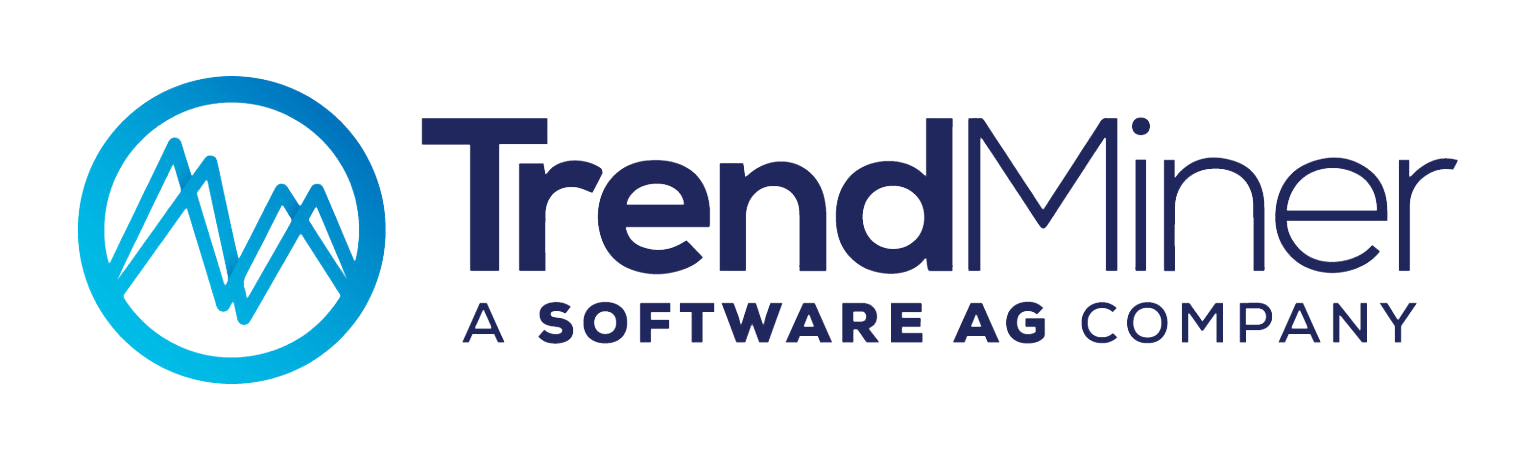
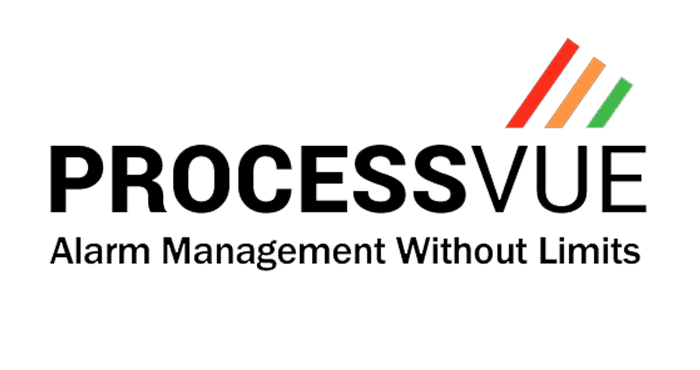
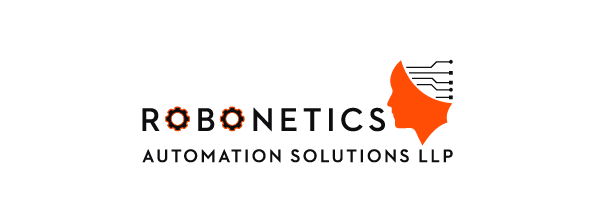
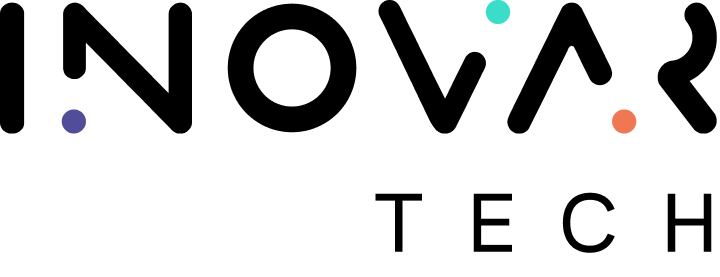